Management is doing things right. Leadership is doing right things.– Peter F. Drucker, an American Management Consultant
A neatly setup and well-organized shop floor can be easy to manage. It saves time and efforts because the workers find their tools at a proper place, equipments are in a healthy condition, floor space is clean from oil, dust or grease, and the shop floor control systems are perfectly tuned to the production operations. Neatness and orderliness on the shop floor leads to happy workers and supervisors, which generates increased productivity. In addition, it sends a message about product quality to the clients and the customers.
What is Shop Floor Management Setup?
The shop floor set up includes setting up machines, assembly lines, tools, storage area, scheduling of operations and setting up control system that records the processes.
Setting up Machines, Equipment and Tools
Machines and equipment are arranged for optimum work flow. Space between machines is kept adequate so that there would be minimum conveying, minimal waste with maximum safety. The loose tools should be placed in the area which is specially allocated for tools, so that they do not go missing. The tools are also arranged as per their size and other conventions, then it is easy to find out a missing tool faster.
Setting up Assembly/Production Lines
This type of assembly line should be wisely selected depending on the type of production. The production line processes are closely observed to simplify complicated processes and remove unnecessary processes. The area around the assembly line is kept adequate for the movement of workers, inventory and equipment.
Scheduling Shop Floor Operations
Since the shop floor works 24X7 in three shifts, scheduling is vital for a seamless production process. The scheduling of operations includes machine scheduling such as single and parallel machines, job scheduling that requires to schedule the jobs as per their level of urgency and scheduling of workers and staff as per their availability.
Setting up Storage Area
The storage area of the shop floor stores raw material, the intermediate material and the inventory. The storage of inventory should be well organized and well-documented. The material of the same type should be grouped together. The material required for the same process or task should be placed together.
The ready product should be placed on the racks or in cabinets. The track of the material and the ready products should be recorded.
Work Center VS Resource Center
Let us now understand the difference between a work and a resource center.
Work Center
A Work center is a section of production line where the workers carry out manufacturing activities or all the tasks associated with a single process. For example, the car production line would have multiple work centers such as welding, fixing, gear-box and painting.
Each work center has skilled workers, equipment, raw material and work area allotted to it. The work centers are expected to perform various work associated to a single type of task or a process.
Resource Center
A resource center provides information on the business, flagship product and other product variants, brand and other activities. It keeps a collection of online product catalogues, instruction manuals, user guides and details of a product dealer. The resource center also publishes news and white papers.
Shop Floor Management Activities
Following are two fundamental activities the manager carries out on the shop floor −
- Daily Activities
- Continual (Kaizen) Activities
Let us now discuss them in detail for better understanding.
Daily Activities
The daily activities that a manager does on a shop floor includes:
- Daily team meetings.
- Directly manage all the resources at hand.
- Gemba walk: Managers walking on the shop floor for monitoring if everything is going on smoothly or not, increases the morale and safety of workers and in turn the productivity.
- Practical problem solving and taking corrective action on faulty machines.
- Housekeeping for cleanliness and orderliness.
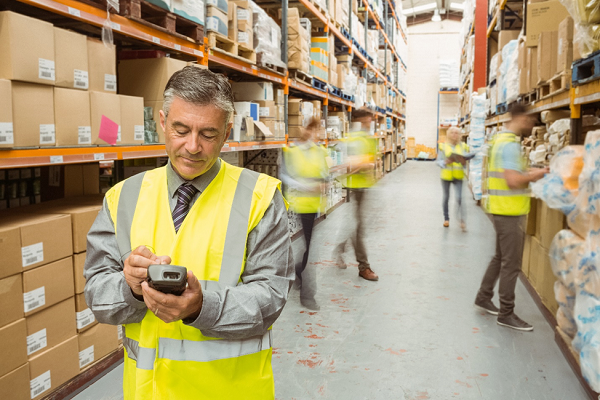
Continual (Kaizen) Activities
These activities include −
- Addressing current problems, anticipating any future problem related to processes, activities, methods, machines and workers.
- Taking preventive measures on the potential upcoming problems to avoid loss of time and safety.
- Continually updating self on knowledge about new machines, tools and techniques for improvement of the shop floor is essential.
- Notifying and discussing with the higher management about any major change if required on the shop floor.
- Keeping liaison with workers, subordinates and suppliers.
In the next chapter, we will discuss in detail about Shop Floor Control.
Comments
Post a Comment