Six Sigma - Control Phase
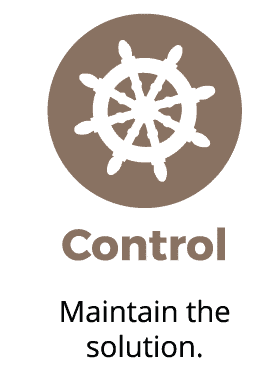
The last phase of DMAIC is control, which is the phase where we ensure that the processes continues to work well, produce desired output results, and maintain quality levels. You will be concerned with four specific aspects of control, which are as follows.
Quality control
The ultimate purpose in control is the overall assurance that a high standard of quality is met. Customer's expectations depend on this, so control is inherently associated with quality.
Since the purpose of Six Sigma is to improve the overall process by reducing defects, quality control is the essential method for keeping the whole process on track; for enabling us to spot trouble and fix it; and for judging how effectively the project was executed and implemented.
Quality is at the heart of Six Sigma philosophy. Reducing defects has everything to do with striving for perfection. Whether we reach perfection or not, the effort defines our attitude toward quality itself.
Standardization
Standardization enables processes to go as smoothly as possible. In a manufacturing environment, the value of standardization has been proven over and over.
We need to devise a control feature to processes so that the majority of work is managed in a standardized manner.
Control Methods and Alternatives
The development of a new process of any change to an existing process requires the development of procedures to control work flow.
When a process cannot be managed in the normal manner, we need to come up with alternatives, short of forcing compliance to the standardized method.
Responding when Defects Occur
The final step in a control process is knowing how to respond once a defect is discovered. The weak links in the procedure, where defects are most likely to occur, can and should be monitored carefully so that defects can be spotted and fixed before the process continues.
The response to a defect may be to prevent a discovered flaw from becoming a defect at all. In the best designed systems, defects can be reduced to near zero, so that we may actually believe that Six Sigma can be attained.
Conclusion
The project team determines how to technically control the newly improved process and creates a response plan to ensure the new process, and also maintains the improved sigma performance.
The 'Control Chart' is one of the most widely used quality tools. In this tutorial I'll show you how to use it with Microsoft Excel for six sigma projects. Control limit chart - controlling quality by knowing what's normal or typical for given measurement. Many companies use Six Sigma techniques to identify areas for improvement within their organization - such as finding areas where they need better quality control. This content can help with establishing control limits for charts with an X axis (value) and with an R (ranking) axis (see image). Keeping track of your projects can be difficult with tools like Excel or Google Spreadsheets - but don't worry! We have all the tools you need for creating Six Sigma control charts for Excel. control limit chart in excel
ReplyDelete