Six Sigma - Measure Phase
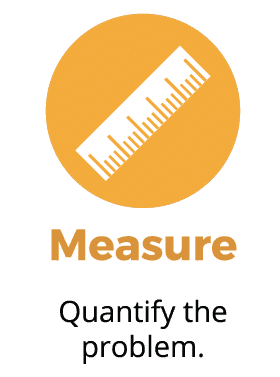
During the Measure Phase, the overall performance of the Core Business Process is measured.
There are three important parts of the Measure Phase.
Data Collection Plan and Data Collection
A data collection plan is prepared to collect the required data. This plan includes what type of data needs to be collected, what are the sources of data, etc. The reason to collect data is to identify areas where current processes need to be improved.
You collect data from three primary sources: input, process, and output.
● The input source is where the process is generated.
● Process data refers to tests of efficiency: the time requirements, cost, value, defects or errors, and labor spent on the process.
● The output is a measurement of efficiency.
Data Evaluation:
At this stage, the collected data is evaluated and sigma is calculated. It gives an approximate number of defects.
● A Six Sigma defect is defined as anything outside of customer specifications.
● A Six Sigma opportunity is the total quantity of chances for a defect.
First, we calculate Defects Per Million Opportunities (DPMO), and based on that a Sigma is decided from a predefined table:
Number of defects
DPMO = ------------------------------------------- x 1,000,000
Number of Units x Number of opportunities
DPMO = ------------------------------------------- x 1,000,000
Number of Units x Number of opportunities
As stated above, the number of defects is the total number of defects found, Number of Units is the number of units produced, and the number of opportunities means the number of ways to generate defects.
For example, the food ordering delivery project team examines 50 deliveries and finds out the following:
● Delivery is not on time (13)
● Ordered food is not according to the order (3)
● Food is not fresh (0)
So now, DPMO will be as follows:
13 + 3
DPMO = ----------- x 1,000,000 = 106,666.7
50 x 3
DPMO = ----------- x 1,000,000 = 106,666.7
50 x 3
According to the Yield to Sigma Conversion Table given, below 106,666.7 defects per million opportunities is equivalent to a sigma performance of between 2.7 and 2.8.
This is the method used for measuring results as we proceed through a project. This beginning point enables us to locate the cause and effect of those processes and to seek defect points so that the procedure can be improved.
Failure Mode and Effects Analysis - FMEA
The final segment of the measure phase is called FMEA. It refers to preventing defects before they occur. The FMEA process usually includes rating possible defects, or failures, in three ways:
● The likelihood that something might go wrong.
● The ability to detect a defect.
● The level of severity of the defect.
You may use a rating scale. For example, rate each of these three areas from 1 to 10, with 1 being the lowest FMEA level and 10 being the highest. The higher the level, the more severe the rating. Hence, a high FMEA indicates the need to devise and implement improved measuring steps within the overall process. This would have the effect of preventing defects. Clearly, there is no need to spend a lot of time on this procedure if the likelihood of a defect is low.
Yield to Sigma Conversion Table
Yield %
|
Sigma
|
Defects Per Million Opportunities
|
99.9997
|
6.00
|
3.4
|
99.9995
|
5.92
|
5
|
99.9992
|
5.81
|
8
|
99.9990
|
5.76
|
10
|
99.9980
|
5.61
|
20
|
99.9970
|
5.51
|
30
|
99.9960
|
5.44
|
40
|
99.9930
|
5.31
|
70
|
99.9900
|
5.22
|
100
|
99.9850
|
5.12
|
150
|
99.9770
|
5.00
|
230
|
99.9670
|
4.91
|
330
|
99.9520
|
4.80
|
480
|
99.9320
|
4.70
|
680
|
99.9040
|
4.60
|
960
|
99.8650
|
4.50
|
1350
|
99.8140
|
4.40
|
1860
|
99.7450
|
4.30
|
2550
|
99.6540
|
4.20
|
3460
|
99.5340
|
4.10
|
4660
|
99.3790
|
4.00
|
6210
|
99.1810
|
3.90
|
8190
|
98.9300
|
3.80
|
10700
|
98.6100
|
3.70
|
13900
|
98.2200
|
3.60
|
17800
|
97.7300
|
3.50
|
22700
|
97.1300
|
3.40
|
28700
|
96.4100
|
3.30
|
35900
|
95.5400
|
3.20
|
44600
|
94.5200
|
3.10
|
54800
|
93.3200
|
3.00
|
66800
|
91.9200
|
2.90
|
80800
|
90.3200
|
2.80
|
96800
|
88.5000
|
2.70
|
115000
|
86.5000
|
2.60
|
135000
|
84.2000
|
2.50
|
158000
|
81.6000
|
2.40
|
184000
|
78.8000
|
2.30
|
212000
|
75.8000
|
2.20
|
242000
|
72.6000
|
2.10
|
274000
|
69.2000
|
2.00
|
308000
|
65.6000
|
1.90
|
344000
|
61.8000
|
1.80
|
382000
|
58.0000
|
1.70
|
420000
|
54.0000
|
1.60
|
460000
|
50.0000
|
1.50
|
500000
|
46.0000
|
1.40
|
540000
|
43.0000
|
1.32
|
570000
|
39.0000
|
1.22
|
610000
|
35.0000
|
1.11
|
650000
|
31.0000
|
1.00
|
690000
|
28.0000
|
0.92
|
720000
|
25.0000
|
0.83
|
750000
|
22.0000
|
0.73
|
780000
|
19.0000
|
0.62
|
810000
|
16.0000
|
0.51
|
840000
|
14.0000
|
0.42
|
860000
|
12.0000
|
0.33
|
880000
|
10.0000
|
0.22
|
900000
|
8.0000
|
0.09
|
920000
|
Comments
Post a Comment